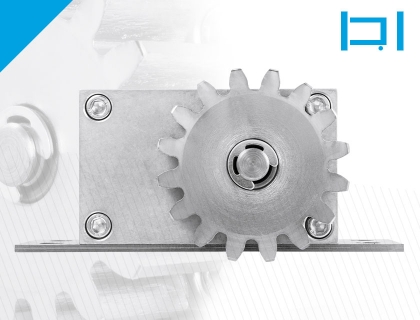
When choosing which automation model to use for a motorised sliding gate, certain elements need to be considered that can affect the correct operation of the system. These elements are: the characteristics and type of gate, how the system will be used including frequency, and external factors such as temperature or structural aspects of the installation site. Regarding this latter aspect we would like to focus on cases in which the sliding gate for automation is located on a slope. When choosing the motorisation unit in these contexts we must first of all consider the forces in play; to do this, one piece of data to be calculated is the size of the angle in degrees in order to determine the power (maximum thrust) needed for the motor to move the gate. We also, however, need to know what other phenomena connected with this particular context can affect the gate's operation. The leaf movement in sliding gates positioned on a slope can be quiet when opening but noisy when closing. In the latter phase, the force generated by the automated movement of the leaf is added to the force exerted by the leaf on the pinion due to the slope and gravity. This “sliding” process leads to an imperfect coupling between the pinion of the motor and the rack, generating noise as well as being dangerous through unexpected and uncontrolled movements of the leaf. Hi-Motions has developed a radial brake (199.1) to solve this issue while the automation unit is in operation, maintaining the same speed on the operator and the gate while descending the slope and applying resistance (7Nm) in the direction of rotation, leaving the opposite side free. In addition to this, accessory 199.1 also gives control over the speed of the leaf even when the automation unit is released, here too reducing the free movement of the leaf to a minimum.